Carbon fiber in structural reinforcement: a sustainable choice
- Cristian Polito
- Apr 23, 2024
- 4 min read
Dear readers, Today we want to talk about a topic of great importance in the construction and infrastructure sector: the use of carbon fiber in structural reinforcement.
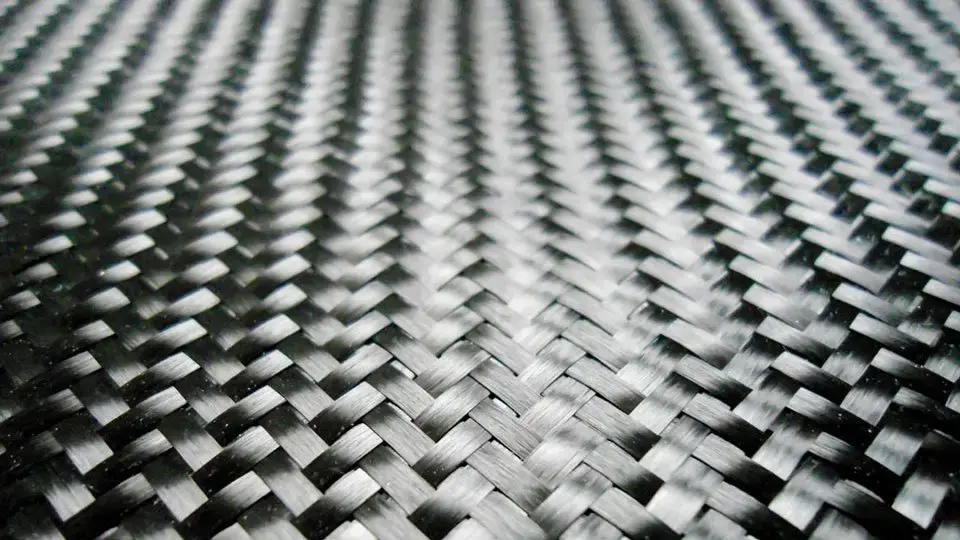
Foreword
Carbon fiber originates from a complex chemical process involving the polymerization of carbon-rich organics. This process begins with the conversion of carbon-rich raw materials, such as polyacrylonitrile (PAN), coal or oil, into carbon filaments through a high-temperature heat treatment known as carbonization.
First, polyacrylonitrile (PAN) undergoes a wet or dry spinning process to create filaments. These filaments are then dried and stretched into thin sheets. They are then heated to very high temperatures in an oxygen-free environment, usually in the range of 1,500 to 3,000 degrees Celsius, so that oxygen and other noncarbon elements in the material are removed, leaving behind purified carbon filaments. Once produced, these filaments are woven together to form carbon fabrics, which can be used in a variety of industrial applications. Depending on the manufacturing process and the composition of the starting material, different types of carbon fiber with different mechanical and chemical properties can be obtained.
Importantly, the carbon fiber development process was a team effort involving numerous experts in different scientific and technological fields, contributing to the creation of one of the most revolutionary materials of the 20th century.
From motorsport to daily life
Today, carbon fiber is widely used in the creation of a wide range of materials. In the world of motorsport and in many adrenaline sports activities, the goal has always been to develop technologies capable of ensuring ever lighter, more dynamic and stronger materials. One of the secrets behind the extraordinary performance of Formula 1 cars lies precisely in carbon fiber. First introduced in 1981 with the McLaren MP4/1 car designed by John Barnard, this material revolutionized the industry. Since then, crashes have become less impactful and vehicles have become more resistant to flames in spectacular crashes.
As is often the case, innovations from extreme sports and the military also find application in the civilian arena. Carbon fiber has made its way into everyday life because of its proven utility and the strength of its component materials. From an object of study in materials science and technology, it is now used on a large scale in industrial production: it is mainly used to reinforce composite materials by aggregating with two or more materials, such as plastic polymers or metals.
Having become increasingly popular in recent years due to its exceptional properties and environmental sustainability, we will explore how carbon fiber contributes to sustainability in structural reinforcement and what advantages it offers over other traditional materials.
Sustainability in structural reinforcement
1.Lightness and Strength
The main advantages of carbon fiber are its extraordinary lightness, biocompatibility, and strength. This material offers superior strength compared to other materials such as steel, while being much lighter. This reduces the overall weight of structures, resulting in less demand for raw materials and less consumption of natural resources.
2. Durability and Longevity
Structural reinforcements made with carbon fiber are extremely durable and have a long service life. This means that carbon fiber reinforced structures require less maintenance over time, helping to reduce the environmental impact associated with frequent replacement or repair of materials.
3. Energy consumption
The production of carbon fiber requires less energy than other traditional materials such as steel or cement. In addition, carbon fiber production processes can be optimized to further reduce energy consumption and greenhouse gas emissions.
4. Recyclability
Although it is a complex material to recycle, there are evolving technologies that allow carbon fiber to be recovered and recycled from obsolete or damaged structures. This helps reduce the environmental impact of producing new materials and promote a circular economy.
5. Energy performance
The use of carbon fiber in structural reinforcement can lead to improved energy efficiency through weight reduction and the possibility of designing innovative and sustainable solutions.
Choosing the best material for structural reinforcements depends on the specific needs of the application, including the expected load, operating environment and strength requirements.
However, carbon fiber is often considered one of the best materials for structural reinforcement in many applications by offering a unique combination of light weight, high strength, stiffness and corrosion resistance, making it ideal for a wide range of applications, from automotive and aerospace to civil engineering and boat building.
Other materials such as fiberglass, steel, aluminum, and ceramic matrix composites may be more suitable in certain circumstances, so it is important to carefully evaluate the options based on the specific needs of the project.
Fiberglass: Fiberglass is one of the most common materials used for structural reinforcement. It has good tensile strength and can be used in a variety of applications, including reinforcement of concrete elements, pipes and plastic structures.
Aramid: Aramid fibers, such as Kevlar, are known for their high strength and light weight. They are often used in applications that require protection against impact and abrasion, such as in automotive and warfare applications.
Fiber Reinforced Polymers (FRP): These composite materials combine polymer resins with reinforcing fibers, such as fiberglass or carbon fiber. They are used to reinforce concrete, wood and metal structures, offering increased strength and durability.
Steel: Steel is a traditional material for structural reinforcement and is widely used in construction. It can be used in the form of steel bars for reinforcing concrete or as stand-alone structural elements.
Aluminum: Aluminum is another commonly used material for structural reinforcement, especially in aerospace and automotive applications. It offers good corrosion resistance and a high strength-to-weight ratio.
Ceramic matrix composites: These materials combine reinforcing fibers with a ceramic matrix to create a lightweight and strong material. They are often used in high-temperature applications, such as in aerospace and automotive.
In light of these considerations, if you are looking for structural reinforcement solutions that offer light weight, strength and durability, Holson is here for you. With 40 years of experience in composite materials and anticorrosive coatings, we can carefully study your projects and propose the best solutions based on your specific needs. Whether you need reinforcements for industrial, civil, aerospace or marine applications, we are ready to put our expertise and know-how at your disposal to ensure excellent results.
Contact us today to find out how we can help you implement your projects successfully!
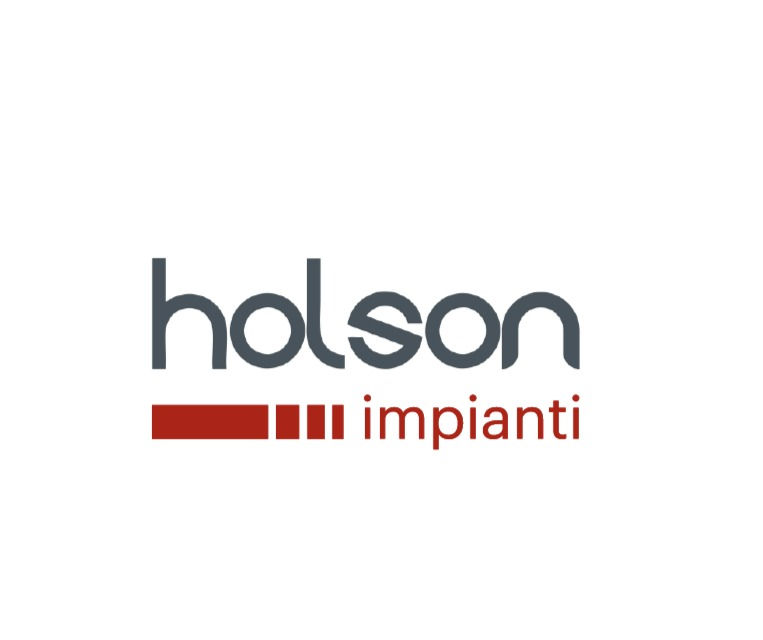
Comentarios